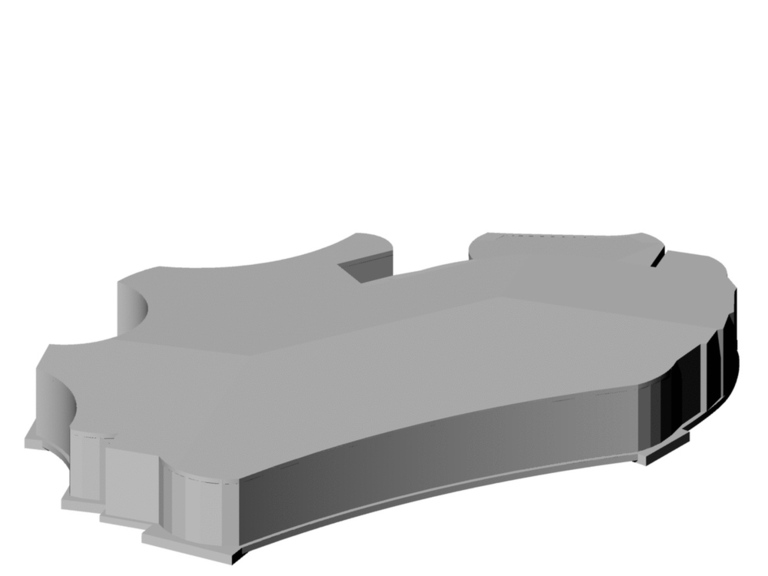
Rendering of the reinforced concrete integrated foundation/basement system or “subfloor” to which the Chrysalis steel frame is attached. (Click for a higher-resolution version.) Most of this structure is underground. Compare to the first figures of the two previous articles of this series. Image © 2015 Arup; used with permission,
tl;dr: I present more details on the Chrysalis integrated foundation/basement system (“subfloor”) and other construction at the Chrysalis site, featuring the work of Whiting-Turner.
This article is one in a series exploring in depth the creation of the Chrysalis amphitheater in Merriweather Park at Symphony Woods in Columbia, Maryland. For the complete list of articles please see the introduction to the series.
The previous two articles in this series discussed the fabrication and installation of the steel frame and skin of the Chrysalis. This article presents more information on the construction of the structural concrete integrated foundation/basement system (also known as the “subfloor”) to which the steel frame is attached. It features the work of the Whiting-Turner Contracting Company of Towson, Maryland.1
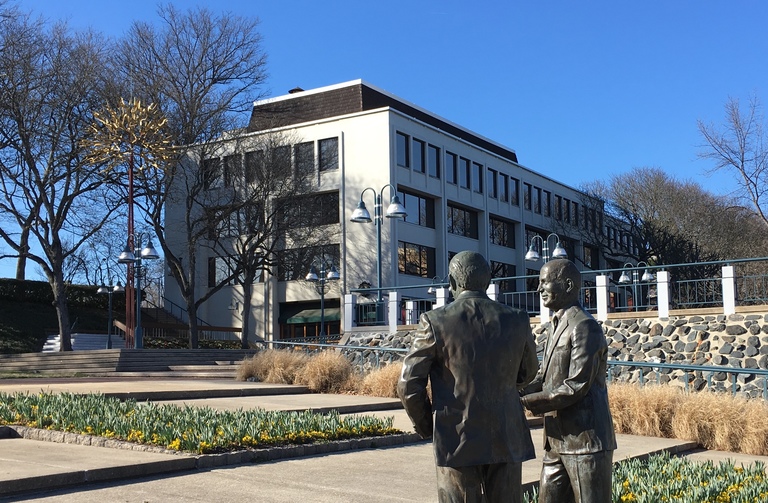
The Teachers Building at 10221 Wincopin Circle (completed 1967), constructed by Whiting-Turner as the first office building in Columbia, Maryland. (Click for a higher-resolution version.) Image © 2017 Frank Hecker; available under the terms of the Creative Commons Attribution 4.0 International License.
Whiting-Turner
As discussed in the previous article, for the steel frame and aluminum shell of the Chrysalis the Inner Arbor Trust used A. Zahner Company as the “design-build” contractor. For the remainder of the Chrysalis construction, including construction of the reinforced concrete structural “subfloor” that serves as a robust foundation beneath the Chrysalis stage, the Trust followed the more traditional “design-bid-build” process. After competitive bidding the Trust selected as general contractor the Whiting-Turner Contracting Company of Towson, Maryland.
Like Zahner, Whiting-Turner is a private company with a heritage that reaches back over a hundred years. It was founded in 1909 in Baltimore, Maryland, by G. W. C. Whiting, a Baltimore native and recent graduate in civil engineering from the Massachusetts Institute of Technology, and his classmate LeBaron Turner. Turner left the company after five years, but Whiting continued his association with the company until his death in 1974 at the age of 91.
In its early days Whiting-Turner bid on contracts for paving roads and laying sewer pipes. In the 1920s it took on bigger projects, including the elevation of Loch Raven Dam in Baltimore (completed 1922) and the construction of various bridges. (Whiting-Turner later did work on both the Chesapeake Bay Bridge and the Delaware Memorial Bridge.)
1938 saw Baltimore native and Johns Hopkins engineering graduate Willard Hackerman join Whiting-Turner. After rising through the ranks Hackerman replaced G. W. C. Whiting as president in 1955, and remained in that position until his death in 2014 at the age of 95. (His replacement was current president and CEO Timothy Regan.) During Hackerman’s tenure Whiting-Turner literally changed the face of Baltimore, constructing (among others) Meyerhoff Symphony Hall, the National Aquarium, M&T Bank Stadium (home of the Baltimore Ravens), and (last but not least) Jim Rouse’s Harborplace development.
Closer to home, Whiting-Turner constructed the Teachers Building (completed 1967), the first office building in Columbia and the former headquarters of the Columbia Association. Whiting-Turner also built the Columbia Mall (completed 1971) and oversaw its later expansion and renovation as The Mall in Columbia (completed 1999).
Whiting-Turner’s involvement with Columbia is thus as old as the city itself, and its work on the Chrysalis marks 50 years of Whiting-Turner projects in downtown Columbia.
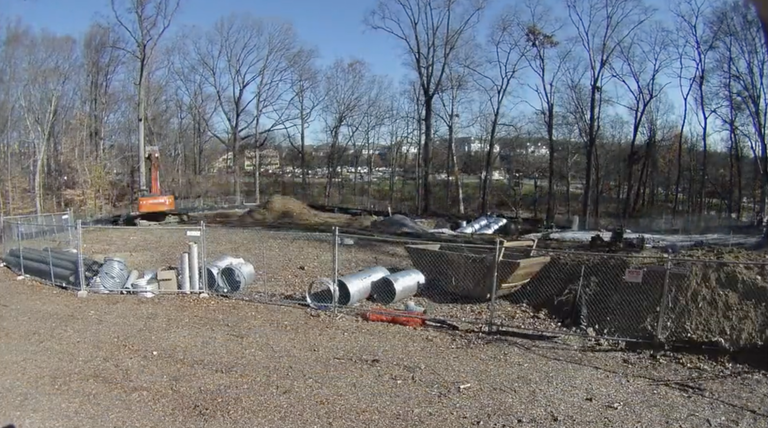
The Chrysalis construction site in the early stages of site preparation and grading. (Click for a higher-resolution version.) Note the cistern under construction at the back of the site. (See also the figure below.) Image © 2015 Inner Arbor Trust; used with permission.
Preparing the Chrysalis site
Whiting-Turner’s role in the construction of the Chrysalis encompassed more than just the construction of the foundation/basement: they were ultimately responsible for tree protection, stormwater management, site utilities, electrical, plumbing and HVAC systems, roads and paths, and general site work—things that most users of the Chrysalis will likely not consciously notice, but which are critical to ensuring the safety, stability, and functioning of the Chrysalis as a whole.
As the general contractor Whiting-Turner selected and oversaw subcontractors who carried out these various tasks. However in the end it was Whiting-Turner’s work in coordinating the many details of construction and holding subcontractors to high standards of quality that would make the difference in bringing the project to a successful conclusion. This work was overseen by Whiting-Turner vice president (and Howard County resident) Jeff Cooper, project manager Peter “Tyge” Sheehan, and assistant project manager Sam Grayman.
After the Chrysalis groundbreaking in September 2015, Whiting-Turner established its on-site office and commenced preparing the site, once the Inner Arbor Trust had received a grading permit from Howard County. (This was separate from the building permit, which was issued later.)
Appropriately, given the concern expressed by many regarding the trees of Symphony Woods, Whiting-Turner’s first task was to ensure the health of trees near the construction area. In pursuit of this they hired a professional arborist to survey the trees in the vicinity and create a comprehensive plan to protect them. This included pruning the roots of trees next to areas scheduled to be excavated, placing mats to protect specific critical root zones, and doing nutrient feeding for certain key trees.
There is a small stream to the north of the Chrysalis and behind the Chrysalis to the east (toward South Entrance Road). In order to limit runoff and prevent construction debris from entering the stream buffer area, “super silt” fencing (filter fabric backed by chain link fencing) was placed around the construction area.
The next task was the construction of a new 8-inch water line to the Chrysalis site itself and to the Chrysalis service road (which runs from the Merriweather Post Pavilion VIP parking lot to the back of the Chrysalis). This water line serves fire suppression sprinklers in the Chrysalis itself, and supplies two new fire hydrants at the beginning and end of the Chrysalis service road. The line will also supply drinking water for general purposes in and around the Chrysalis, and provide water to subsequent phases of Merriweather Park at Symphony Woods.
The construction of the water line illustrates the complications of land ownership in the Merriweather-Symphony Woods neighborhood. The source of the water for the new water line is an existing water main in South Entrance Road, and the new line passes under Symphony Woods Road, a private road owned by the Howard Hughes Corporation. Howard Hughes provided the Inner Arbor Trust an easement to make such a connection as part of a wide-ranging reciprocal easement agreement concluded between the two parties.
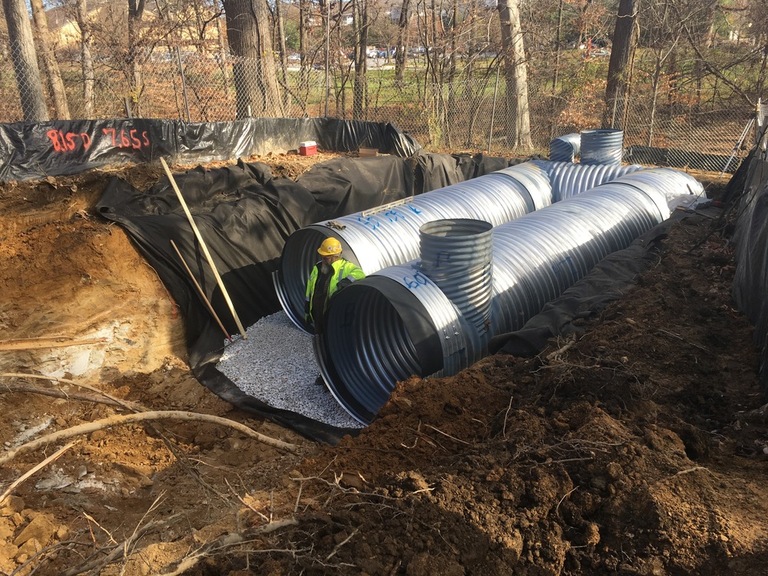
The underground cistern behind the Chrysalis under construction. (Click for a higher-resolution version.) The two vertical pipes (along with another not yet installed) were capped with manhole covers once the cistern was covered and the overlying surface paved. Image © 2015 Inner Arbor Trust; used with permission.
The Chrysalis cistern
As evidenced by the July 2016 flash flood in Ellicott City, heavy rainstorms can result in very large quantities of runoff, especially when the rain falls onto impervious surfaces such as roads and buildings. A key task in construction, undertaken even before excavating the site, was therefore putting in place permanent measures to handle runoff into the nearby stream, particularly from the 12,000 square feet of the Chrysalis shell canopy—a pleated surface that acts as a very large rain gutter over the approximately 5,000 square feet of the Chrysalis stage.
On many building sites ponds are constructed to retain runoff prior to releasing it into the surrounding watershed. Aesthetic considerations and the limited area of the site required a different solution for the Chrysalis: instead of a pond Whiting-Turner installed an underground cistern, constructed of large corrugated metal pipes 5 feet in diameter and capable of storing almost 2,500 cubic feet of water in total (over 18,000 gallons).
The pleats of the Chrysalis shell carry rainwater and snow melt to the base of the nine shell legs where the canopy comes to the ground. At the base of each leg stormwater drains through beds of landscaping stone that sit on galvanized steel grates that top underground basins. The basins (resembling concrete bathtubs) then funnel the runoff into a network of underground pipes that empty into the cistern.
The runoff accumulates in the cistern until the cistern reaches its design capacity, at which point the cistern begins to release water into the stream system. The overall effect is to even out the flow of water and reduce high-velocity surges during severe downpours. This reduces the harmful effects of both local erosion of the stream bed and downstream sedimentation as the runoff proceeds into the Little Patuxent watershed.
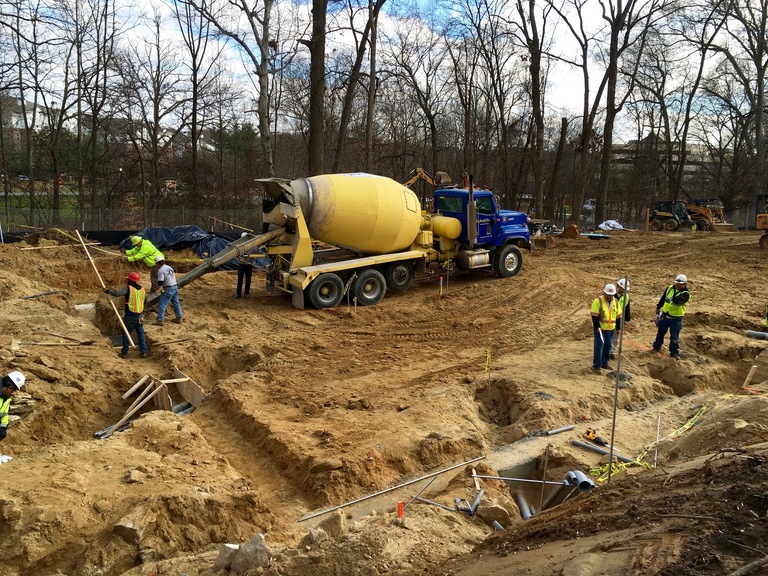
Pouring a concrete “mud mat” in preparation for constructing the walls of the structural subfloor. (Click for a higher-resolution version.) The view is from the front of the Chysalis (stage right of the alpha stage) looking southeast. A completed mud mat is in the foreground, with previously-installed utility conduits running under the completed mat and the one being poured. Image © 2015 Inner Arbor Trust; used with permission.
Site excavation and mud mats
After the cistern was installed Whiting-Turner began the mass excavation of the Chrysalis foundation/basement, preparing the site for the foundation construction and for installation of underground utilities, including conduits for supplying electricity to the theatrical lighting and audio systems.
The Chrysalis construction site was designed as closely as possible to be in a “net zero fill” condition. In other words, earth that was removed during the initial stages of construction was saved and then redeployed later in the construction process, instead of being hauled away. This was more cost efficient and also resulted in a lower carbon footprint for the construction as a whole.
As part of this process dirt and small stones were stockpiled on-site and covered with plastic for future use in backfilling the inside and outside of the Chrysalis foundation walls. Larger stones that could not be used for fill were removed by Whiting Turner’s subcontractor, Highland Turf, Inc., and moved to other locations within the Merriweather-Symphony Woods and Crescent neighborhoods, for use by the Howard Hughes Corporation in its own stream restoration projects.
Once the foundation was excavated, workers poured concrete “mud mats” (also known as “mud slabs”) following the outline of the Chrysalis’s exterior and interior walls. The mud mats served as a non-structural “foundation for the foundation,” providing a solid flat surface upon which reinforcing steel bars (rebar) and wooden molds for concrete (formwork) could be placed, and the concrete for the subfloor’s walls then poured.
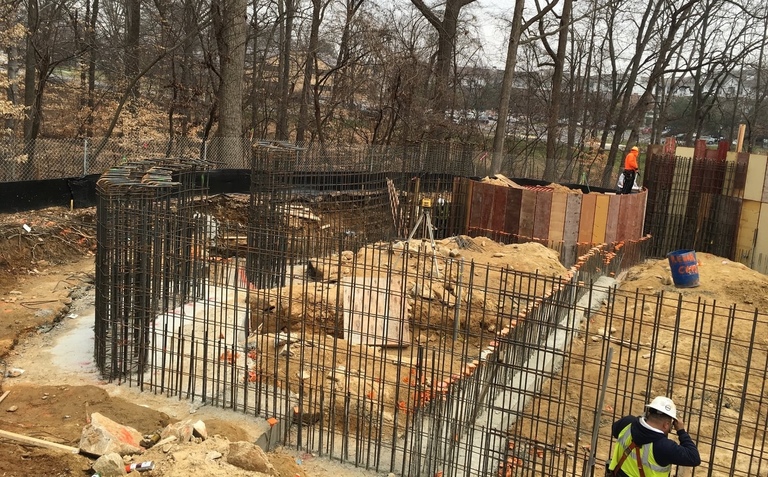
Rebar in place prior to completing the wooden formwork and pouring concrete for the subfloor walls and piers. (Click for a higher-resolution version.) The view is from the front of the Chrysalis (stage right of the alpha stage) looking northeast. The heavy concentrations of rebar to the left and elsewhere are for the concrete piers to which the legs of the Chrysalis steel frame are attached. Note the two layers of rebar for the exterior wall, as well as the use of orange “rebar caps” to protect workers from exposed rebar. Image © 2015 Inner Arbor Trust; used with permission.
Reinforced concrete
Once the mud mats were poured, workers placed reinforcing steel bars or rebar in preparation for constructing the exterior and interior walls of the subfloor foundation.
First used extensively in the 19th century and perfected in the 20th, reinforced concrete is ubiquitous in modern construction. It works by combining the compressive strength of concrete with the tensile strength of steel—in other words, the concrete resists being pushed together and the steel resists being pulled apart. With the two bonded together in a composite, the resulting material resists loads placed on it without bending or breaking.
The reinforced concrete used in the Chrysalis is “cast in place” concrete: A mesh or “mat” of rebar was laid on top of the previously-poured mud mats, tied together, and inspected. The rebar was laid especially densely in areas designed to bear heavier loads, such as the concrete piers to which the legs of the Chrysalis steel frame are attached. (See the figure above.)
Wooden modular paneled formwork was then constructed around the rebar to act as a mold, and high-strength “5,000 psi” concrete poured into the formwork and around the rebar.2 As the concrete cured it bonded to the steel bars (rebar is typically corrugated to make this bond stronger), giving the resulting walls or piers their strength.
Laying the rebar, constructing the formwork, and pouring concrete was made more complicated by the irregular shape of the Chrysalis foundation: looking at the structure from above (in so-called “plan view”) there are only four 90-degree angles apart from the stairs. In all other places the formwork needed to be carefully framed to correspond to the curves in the exterior walls and piers.
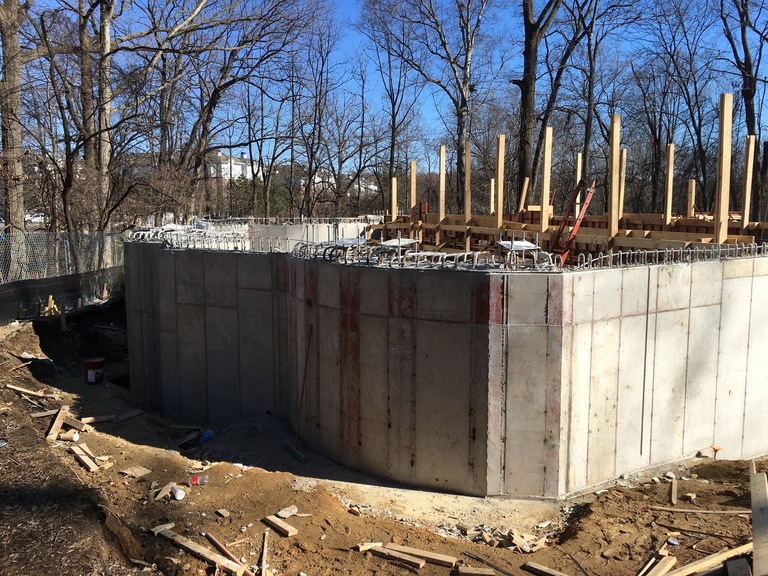
Exterior wall of the Chrysalis subfloor after pouring concrete, and wooden formwork for the interior walls. (Click for a higher-resolution version.) The view is from the front of the Chrysalis (stage right of the alpha stage) looking southeast. The wall to the right is the same as shown in the foreground in the previous figure, while the pier in the center is the same as that shown in the left of the previous figure. Image © 2016 Inner Arbor Trust; used with permission.
The foundation/basement walls and ceiling
In January 2016 construction of the Chrysalis was interrupted by the “Snowzilla” storm. After the storm was over and snow cleared from the site, the first major concrete pour of the foundation was successfully made, by Whiting-Turner’s subcontractor McGuire Concrete. First to be poured were the 8-inch-thick exterior walls and the associated concrete piers for attachment of the steel frame of the Chrysalis.
The exterior walls were reinforced with #3 and #5 rebar placed every 6 inches, laid crossways in two layers.3 The piers were reinforced with a larger size of rebar, laid so densely that special accomodations had to be made to fit in the anchor bolts to which the legs of the steel frame were attached.
(Special care was taken in surveying where to place these bolts, in order to position them as accurately as possible for connecting to the steel frame. The bolt positions were surveyed twice before pouring the concrete, and then surveyed again immediately afterward to ensure that the pouring operations had not disturbed them.)
Subsequently three interior walls were poured (also 8 inches thick, and similarly reinforced), running in parallel lines from the front of the Chrysalis to the back. These walls formed two interior rooms of a walkout basement, one to be used for electrical equipment providing 2,000 amps to the stage, and the other to be used for storage of Chrysalis-related equipment—almost 1,600 square feet in all.
In the back of the Chrysalis Whiting-Turner and its subcontractors constructed three sets of concrete stairs leading from ground level to stage level, for the use of performers, stagehands, and others. (Between the stairs is a loading dock with a space for a so-called ”scissors lift” to lift equipment from the dock to the stage.)
Once the interior walls were complete, the two basement rooms were covered with a 10-inch-thick slab of reinforced concrete, poured into formwork supported from below, with two layers of #5 rebar placed every 6 inches each way. This slab forms the ceiling for the basement rooms and a portion of the concrete floor for the stage.
The remaining spaces outside the two rooms were then filled with dirt saved from the earlier excavation, topped with a layer of gravel, and then capped with 10-inch-thick slabs of reinforced concrete to match up with the slab over the basement rooms. All of these slabs tied directly into the walls and piers, using rebar exposed for this purpose. (See the figure below.)
In total about 550 cubic yards of high-strength 5,000 psi concrete went into the structure. The concrete was reinforced by over 100,000 pounds of rebar.
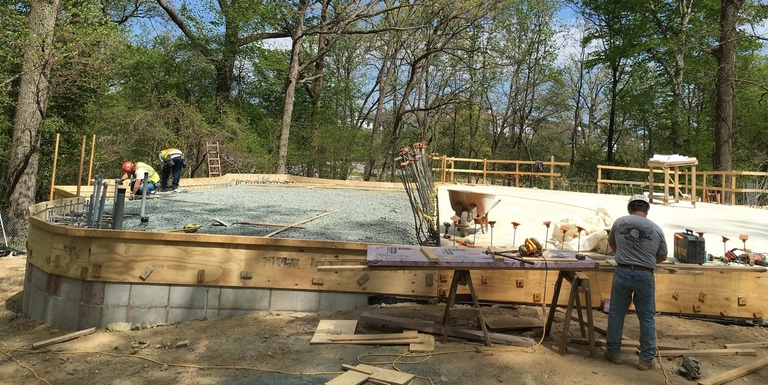
Workers preparing wooden formwork in preparation for pouring one of the reinforced concrete slabs forming the top of the subfloor. (Click for a higher-resolution version.) The view is from the front of the Chrysalis looking east. The pier to the left is the same as that shown in previous figures. Note the exposed rebar on the perimeter walls, the piers, and the already-poured slab over the basement, as well as the utility conduits at the left. Image © 2016 Inner Arbor Trust; used with permission.
The structural diaphragm
As previously discussed, all of these elements form what structural engineers call a “diaphragm,” integrating the vertical foundation walls and piers together with the horizontal floor into a single, strong structural whole. This is the same principle that makes a soup can much stronger with one of its lids fully attached to its cylinder, as the lid acts as a diaphragm, transferring forces exerted from one point throughout the rest of the can. The result is a strong rigid structure that can easily support the steel frame of the Chrysalis and the attached shell, and help the Chrysalis resist the various loads placed upon it.
Whiting-Turner’s role in constructing the Chrysalis did not end with the completion of the subfloor. As a general contractor its work is not finished until the completed Chrysalis structure and all related elements—railings, roads, pathways, etc.—are handed over to the Inner Arbor Trust. Discussion of the remaining elements, including some not yet finished at the time of writing, is deferred to a future article on the architectural details of the Chrysalis and the lansdcaping of its surroundings.
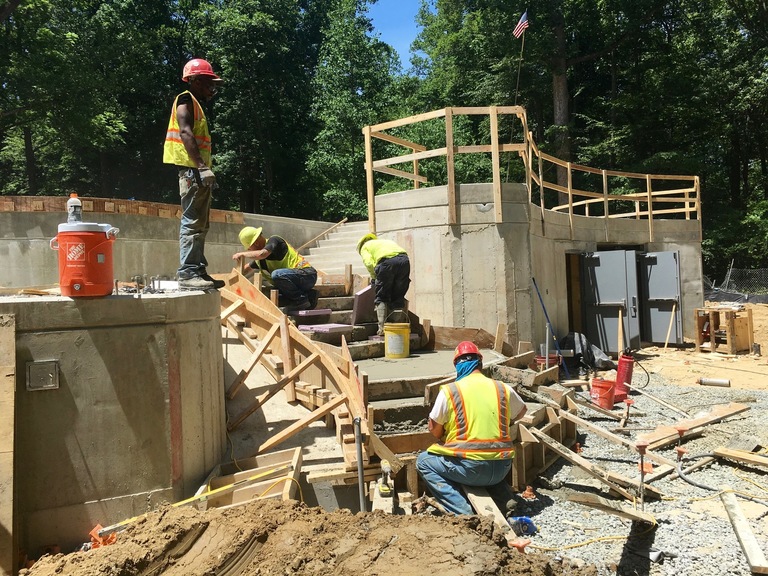
Workers pouring concrete for the stairs at the back of the Chrysalis. (Click for a higher-resolution version.) The worker to the left is standing on one of the reinforced concrete piers of the Chrysalis; to the right are the doors leading into the two basement rooms of the subfloor. Image © 2016 Inner Arbor Trust; used with permission.
For further exploration
This article is based on material from a variety of online and offline sources, including the following:
For more on Whiting-Turner, its history, its work on the Chrysalis project, and related topics, see the following:
- Whiting-Turner portfolio of selected projects and areas of expertise.
- “Whiting-Turner History.” Historical timeline on the Whiting-Turner web site.
- “G.W.C. Whiting rites tomorrow,” page A17, Baltimore Sun, November 19, 1974. Obituary for G. W. C. Whiting.
- “Construction Magnate and Philanthropist,” by Jacques Kelly, page A1, Baltimore Sun, February 11, 2014. Obituary for Willard Hackerman.
- “Building Occupancy,” page F10, Baltimore Sun, September 17, 1967. Announcement of the opening of the Teachers Building in Columbia.
- “Work Sped On Columbia Mall for Tomorrow’s Opening,” by Carleton Jones, page F1, Baltimore Sun, August 1, 1971. An article on the opening of the Columbia Mall.
- “New wing of The Mall opens with a flourish,” by Jill Hudson Neal, page 14B, Baltimore Sun (Anne Arundel edition), September 19, 1999. The opening of a new wing of The Mall in Columbia after the mall’s renovation and expansion.
- Inner Arbor Trust construction updates for September 2015, October 2015, November and December 2015, January and February 2016, March 2016, and April 2016. Ongoing updates describing the progress of the construction of the Chrysalis.
- “Chrysalis steel and concrete construction.” A collection of photographs (and a video) showing the progress of the construction of the Chrysalis.
- “Reinforced concrete.” A Wikipedia article describing the history and use of reinforced concrete.
For more on the Chrysalis amphitheater and its origins in the Inner Arbor concept plan, see the following:
- Michael McCall presentation of the Inner Arbor concept plan to Leadership Howard County [33-minute video] (September 20, 2013).
- The Chrysalis portion of the Inner Arbor pre-submission community presentation (December 2, 2013).
- Michael McCall presentation to the Howard County Design Advisory Panel [20-minute video] (February 26, 2014).
For more of my opinions on and explanations of various aspects of the Chrysalis and Merriweather Park at Symphony Woods, see the Inner Arbor-related posts in the series “The Inner Arbor plan takes shape” and elsewhere on this blog. (Note that some of these posts contain outdated information relating to park features that were later dropped or revised.)
Portions of this article were adapted (with permission) from the construction updates published by the Inner Arbor Trust. (See the section “Further exploration.”) ↩︎
The strength of concrete is measured in terms of the amount of load it can bear without breaking, as measured in pounds per square inch, with more high-strength mixes costing more. Garden-variety applications like sidewalks typically use less-expensive 3,000 psi concrete. ↩︎
The designations used in the US for rebar correspond to the approximate diameter of the rebar in eighths of an inch. Thus #3 rebar is ⅜ inches in diameter, #5 rebar ⅝ inches in diameter, and so on. ↩︎